Contact Supplier
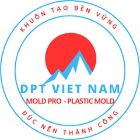
DPT VIET NAM COMPANY LIMITED
The household plastic manufacturing industry is growing strongly with the application of many modern and advanced technologies. Household plastics play an important role in daily life, from small products such as food containers, plastic bottles, to larger items such as plastic tables and chairs and kitchen equipment. This article will analyze in detail the production process of household plastics according to the most modern steps to ensure product quality and save costs for businesses.
1. Choosing the right plastic raw materials
The first step in the production of household plastics is choosing the right plastic raw materials. There are many different types of plastics such as Polyethylene (PE), Polypropylene (PP), Polyvinyl chloride (PVC), and Acrylonitrile Butadiene Styrene (ABS), each with its own properties and specific applications.
Polyethylene (PE): Commonly used in the production of plastic bags, food containers and bottles.
Polypropylene (PP): Preferred in the production of heat-resistant items such as microwave-safe food containers.
Acrylonitrile Butadiene Styrene (ABS): Used to produce products that require high durability such as electronic device casings and toys.
Choosing the right type of plastic not only helps optimize product quality but also helps businesses save on the cost of producing household plastics.
2. Precise mold design
After selecting the raw material, the next important step is mold design. Molds are an important tool to help shape plastic products. CAD/CAM technology is applied to design molds accurately, thereby ensuring that the product meets the requirements of size, shape and aesthetics.
Molds are made from durable materials such as stainless steel or aluminum alloy, helping the mold have a long life in the process of producing household plastics. Modern technologies such as CNC (computer-controlled machining) help process molds with high precision and save time.
3. Injection Molding Process
Injection molding technology is the most popular method in the production of household plastics today. This process begins with melting plastic pellets, then the molten plastic will be injected into the mold at high pressure to create the product.
Steps of the injection molding process:
Melting plastic: Plastic pellets are fed into the machine and melted at temperatures from 200°C to 250°C, depending on the type of plastic used.
Injecting plastic into the mold: Liquid plastic will be injected into the mold through channels at high pressure.
Cooling and solidifying: After the mold is filled, the plastic will be cooled and solidified according to the shape of the mold.
Demolding: The mold is opened and the finished product is pushed out of the machine.
This method has the advantages of fast mass production, consistent quality and cost savings.
4. Post-molding processing
After the product is molded, some additional processing steps may be necessary to ensure that the plastic product meets quality standards. Processing steps may include:
Trimming: Removing excess plastic around the product.
Surface processing: Grinding or polishing the surface to create smoothness and increase aesthetics.
Painting and decoration: If necessary, the product will be painted or decorated to increase its appeal to consumers.
5. Product quality inspection
In the process of manufacturing household plastics, quality inspection is indispensable. Plastic products need to be thoroughly tested for durability, heat resistance, food safety and scratch resistance. Quality management systems such as ISO 9001 or RoHS standards are often applied to ensure that the product meets the requirements before leaving the factory.
6. Packaging and shipping
Finally, after the products have met quality standards, they will be packaged according to customer requirements. The packaging process must ensure that the products are not damaged during transportation, while protecting the products from external factors such as humidity and sunlight.
Benefits of modern processes in household plastic production:
Increased productivity: Technologies such as injection molding and CNC help increase productivity, minimize product defects.
Saving raw materials: New technology helps optimize the use of raw materials, minimizing plastic waste.
Increased aesthetics: Household plastic products are increasingly beautiful and sophisticated thanks to modern production processes.
Conclusion
The modern household plastic production process not only requires precision in each stage but also ensures that the final product is of high quality, aesthetic and safe for consumers. Plastic injection molding technology, mold processing, and auxiliary processing steps all play an important role in creating quality household plastic products. For businesses like DPT Vietnam, grasping and applying advanced production technologies not only helps to improve competitiveness but also meets the increasingly demanding needs of the market.