Contact Supplier
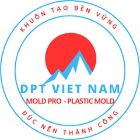
DPT VIET NAM COMPANY LIMITED
Mold making is a crucial activity in the plastic production process. Standard molds will determine the productivity and quality of molded products. In the article below, DPT Vietnam would like to share information about molds and the mold manufacturing process.
Introduction to molds in plastic production
What is a mold?
Simply put, a mold is a metal tool used to shape plastic products. It consists of a cluster of parts assembled together. When plastic is injected, cooled and then pushed out into a product. All plastic products on the market are molded or pressed from molds.
Each mold is manufactured and used for a different product. The size and structure of the mold are determined by the shape, size, quality and quantity of the product to be created.
Mold classification
There are many types of molds on the market today. Depending on your needs, customers can choose the most suitable mold.
- Injection mold
- Compression mold
- Blow mold
- Transfer mold
- Die mold
- Extrusion mold
- Rotary mold
Mold structure
In the mold manufacturing industry, the structure of a plastic mold includes the following basic parts:
Mold body: This is where the mold cavity is located, including two parts: the fixed part and the movable part. The fixed part is mounted on the fixed plate of the plastic injection machine. The movable part is located on the movable plate of the plastic injection machine. The gap between these two parts is filled with molten plastic, then the plastic is cooled to form.
Mold base: This part has the function of clamping the mold tightly into the machine tables when processing the mold.
Guiding and positioning system: The task of the guiding and positioning system is to keep the working position of the two mold body parts when assembled together.
Plastic feeding system into the mold cavity: As the name suggests, its function is to supply plastic from the injection machine to the mold.
Product ejection system: It is responsible for pushing the finished product out of the mold.
Side core system: This part helps remove parts that cannot be removed from the mold by opening the mold.
Ventilation system: The system has the effect of removing the stagnant air in the mold cavity to the outside. From there, the plastic is filled in the mold cavity and the product will not burn or leak air.
Mold cooling system: Has the function of cooling the mold after the processing is completed.
Mold manufacturing process
Input information analysis
Analyzing the input information carefully is the first step in the mold manufacturing process. This information is provided according to the customer's needs and with the advice of the manufacturing unit. Necessary information for input includes:
Mold manufacturing materials.
Number of mold cavities.
Mold type.
Finished plastic material.
Precise requirements for size, gloss or roughness of the surface, ...
Position of the injection pump gate.
Position of the product ejector pin.
Mold design
From the above data, DPT Vietnam's design department will design a mold drawing with full details. On that basis, the production workshop meets and agrees on the structure, processing plan, quality control and mold assembly. From there, a complete mold design is created. This step helps to outline the direction for the production process to be easy and ensure accuracy.
Purchase mold materials and mold components
The next step in mold manufacturing is to purchase mold materials and mold components based on the design drawing. Plastic mold materials are usually metals with high hardness and durability, and can withstand good pressure. In which, steel is a commonly chosen material because it meets the necessary requirements.
Mold manufacturing
Blank manufacturing: The selected steel blocks will be cut into metal parts with standard sizes. In this process, use a milling machine to mill the edges, mill the faces and grind the surfaces to create the outer block mold.
CNC machining: Conduct CNC machining to shape the mold cavity and the mold components. Using a CNC machine will grind the steel blocks according to the exact shape on the design drawing.
Wire cutting machining: Wire cutting machines perform extremely high precision parts, with a tolerance of only 0.005mm.
Electric discharge machining: This step is responsible for shaping in locations where CNC machining or wire cutting cannot be performed.
Finishing machining: In this stage, water will be created, bolt holes will be created, etc.
Polishing the surface of the mold cavity and assembling the mold
Another important step in the mold manufacturing process is surface polishing. The quality of plastic products depends largely on the gloss of the mold cavity, the higher the gloss, the better the quality. Therefore, surface polishing requires meticulousness and precision.
After completing all the mold details, it is necessary to assemble them to create a complete mold. This step also determines the efficiency of plastic production, so it is necessary to ensure high precision.
Mold testing
Conduct mold testing to check the ability to create shapes, dimensional accuracy, and finished product quality. As well as whether the shrinkage, gloss, flatness, etc. of the mold meet the customer's requirements.
Repair and fix any existing problems
At this stage, errors in mold testing will be repaired and fixed by the DPT Vietnam team. After fixing, return to the mold testing step. This ensures that the mold manufacturing process meets the technical requirements according to the input parameters.
Delivering the completed sample to the customer
The completed and qualified mold product will be sent to the customer. DPT Vietnam's mold manufacturing process is meticulous in every step, ensuring to bring the most prestigious and quality products.
Address for cheap, quality mold manufacturing
If you are looking for an address for cheap, quality mold manufacturing, DPT Vietnam is the top suggestion for you. We are confident that we are a reputable manufacturer and processor of all kinds of plastic molds in the market. With 12 years in the industry, DPT Vietnam has gradually improved its production process and service quality to bring the best value to customers.
- DPT Vietnam is a reputable manufacturer and processor of plastic injection molds and plastic molds in the market. We always strive to create quality products to serve customers. Contact us for free consultation on plastic products and molds.
DPT Vietnam Co., Ltd.
a. Field of operation:
Design and manufacture of plastic molds.
Injection molding of plastic products
Repair and maintenance of plastic molds.
b. Contact
Hotline: 0378 972 672 (Mr. Thang) - 0985 074 688 (Mr. Dinh)
Email: dptvietnam@gmail.com