OTIF meaning stands for “On Time, In Full,” a key performance metric introduced by Walmart in 2017 to ensure deliveries meet both timing and completeness standards. By enhancing customer satisfaction and streamlining supply chain efficiency, OTIF helps businesses gain a competitive edge, reduce costs, and improve overall performance.
Nowadays, the significance of on-time delivery cannot be understated. Elevating customer satisfaction through prompt and timely deliveries, while simultaneously enhancing a business’s reputation, forms its undeniable impact.
OTIF definition is considered an initiative by Walmart introduced in 2017, showcasing a meticulously crafted strategy aimed at guaranteeing goods reach customers as specified. As highlighted by Forbes, Walmart has introduced an OTIF target, aiming for 90% on-time delivery and 95% in-full delivery, with these standards taking effect on February 1, 2024. Our mission centers around crafting a thorough roadmap for grasping OTIF. Let’s explore OTIF meaning in the next section.
What is OTIF?
OTIF meaning is often a topic that many people search for. Let’s first look at the OTIF definition before diving deeper.
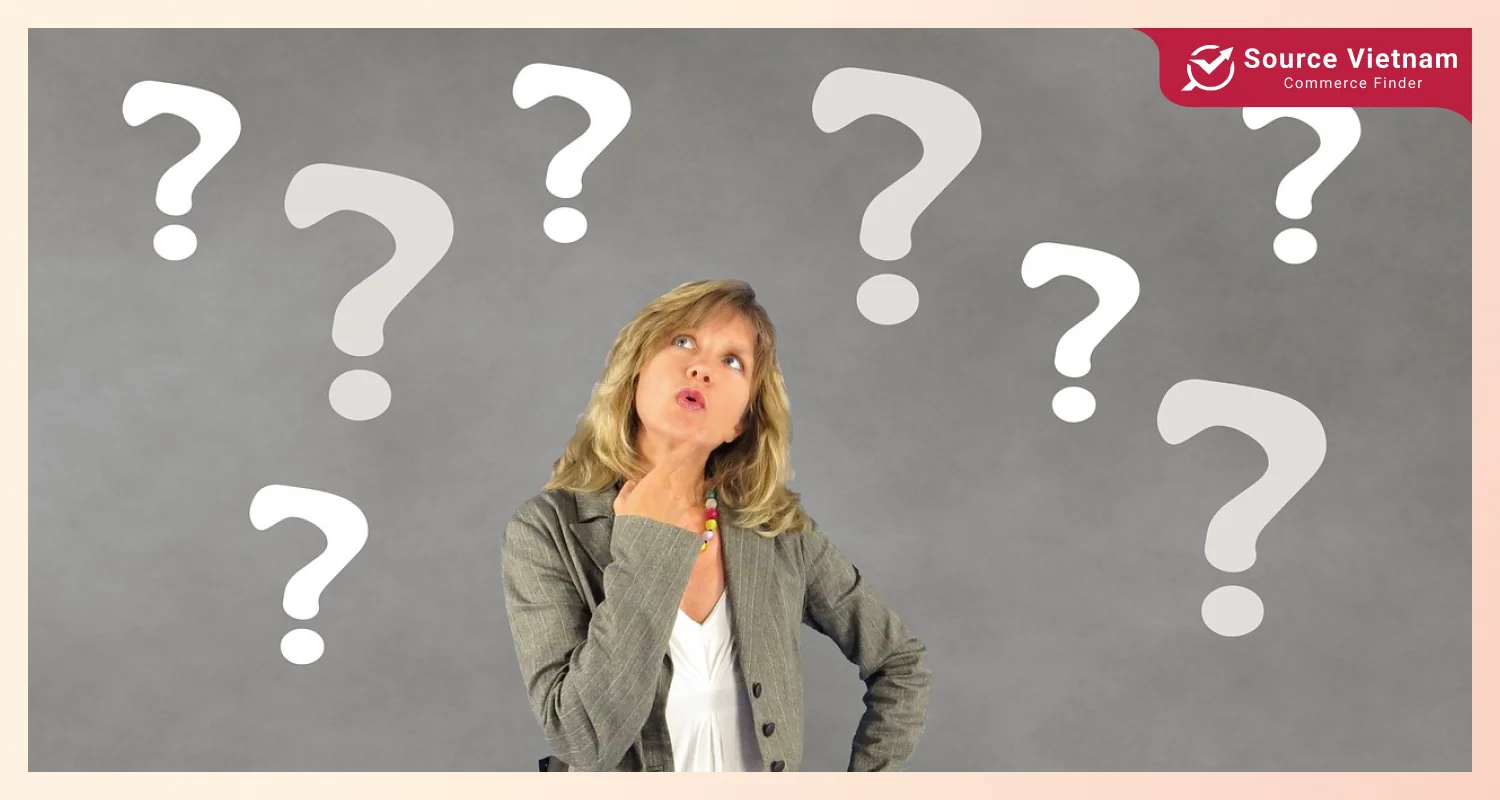
Simply put, this represents one of the key delivery performance metrics. It serves to evaluate effectiveness within supply chain management. It tells you the percentage of orders where suppliers deliver products to customers on time and in full.
OTIF stands for the two phrases “On Time” and “In Full”. They also the two main components of OTIF, specifically:
- On-Time Delivery (OTD): Ensuring deliveries align perfectly with the predetermined schedule.
- Delivery in Full (DIF): Ensuring the customer receives the full order quantity exactly as requested. It lets you know whether the customer received the correct quantity of goods.
OTIF plays many important roles for businesses, including:
- Measuring supply chain performance efficiency.
- Assessing customer satisfaction.
- Indicating overall business performance.
OTIF: A critical metric for supply chain excellence
Read more >>> What is Lead Time? | How to calculate | 5 Types of lead time
Importance of OTIF in the supply chain
Hard to deny the important role OTIF plays in the supply chain. Following the OTIF meaning section, you will discover how this metric improves supply chain performance.

Impact on customer satisfaction
OTIF impacts customer satisfaction by meeting their expectations for timely and complete deliveries. An efficiently operating supply chain significantly elevates the overall customer experience. Suppliers with high OTIF rates gain a significant competitive advantage.
Poor OTIF can lead to several negative consequences:
- Customer dissatisfaction.
- Lost sales.
- Damaged reputation and more.
OTIF as a performance indicator
OTIF is a key performance indicator (KPIs) for supply chain effectiveness and overall operational success. Without overstating, OTIF offers a holistic lens through which supply chain efficiency can be thoroughly assessed.
Helping you identify the areas that need improvement in your supply chain. For example, uncover the reasons behind delayed orders. Certain products may be affected by inventory shortages or other issues. Once problems are identified, they become easier to address.
Industry benchmarks and standards
Each industry operates with its unique set of standards:
- eCommerce and consumer goods: Achieving an OTIF score of 95% or above is generally considered satisfactory.
- Aerospace and automotive: Often deal with more complex products or supply chains. Thus, operate with lower benchmarks.
Companies can utilize OTIF benchmarks to assess their performance and set improvement goals through the following steps:
- Understand the benchmarks: Identify the standards, and whether they align with the company’s current situation.
- Gather data from multiple sources: Analyze the benchmarks thoroughly and consider various influencing factors.
- Set goals: Compare your performance with competitors to determine your position. Adjust targets to ensure they are realistic and appropriate.
- Implement changes: Identify areas needing improvement. Take actionable steps to meet the goals.
- Monitor continuously: Track progress consistently and quickly adapt strategies if ineffective.
How to calculate OTIF
With the OTIF meaning and its significance explained, the next natural question emerges: how to calculate OTIF in supply chain?
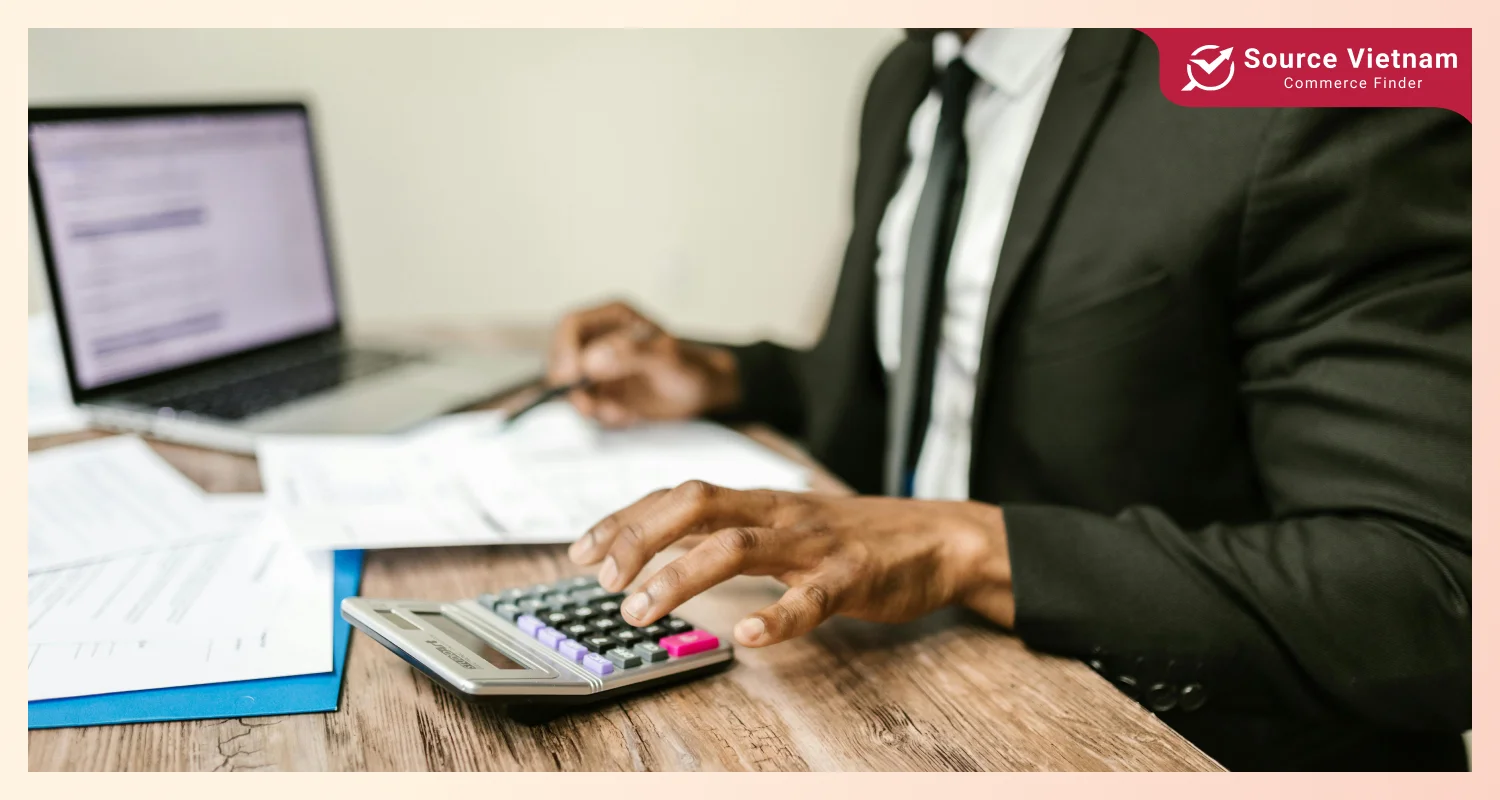
Calculating OTIF is straightforward and follows a simple formula:
OTIF = (Number of orders delivered on time and in full/total number of orders) x 100
Here’s an alternate perspective: Picture a supplier responsible for completing 200 orders in a month. However, only 180 meet the criteria of being delivered both on time and in full.
Therefore, the OTIF calculation would be:
OTIF = (180/200) x 100 = 90%
The final result of this OTIF calculation is 90% for that month.
Achieving a 100% OTIF rate is often regarded as unrealistic. Most businesses set their sights on an 80%-90% range, which is generally acceptable. That said, it’s crucial to ensure this target aligns with the specific goals of each business.
Calculate your OTIF score and improve your supply chain
Read more >>> How to Calculate Total Manufacturing Cost – Full Formula
Benefits of high OTIF scores
The benefits of high OTIF scores in logistics span a wide range. Their key advantages are detailed in the following list.
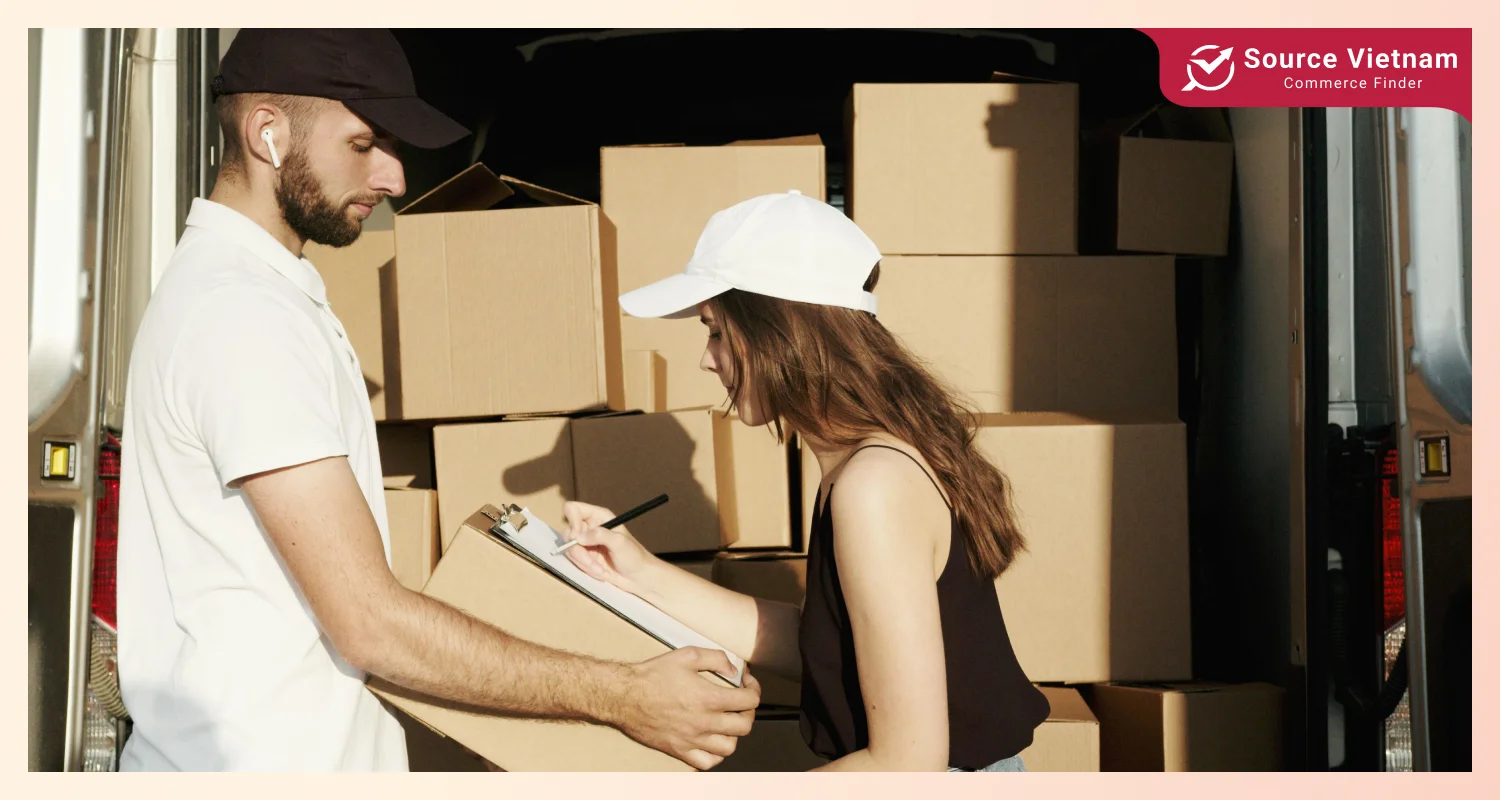
- Improved customer satisfaction: Businesses with high OTIF rates often earn customer satisfaction and positive feedback. By delivering on time and in full, gaining a significant competitive advantage is not hard. Fostering greater customer loyalty.
- Reduced costs: Avoid penalties in cases of late deliveries, reduce return costs, and minimize unnecessary disputes.
- Increased efficiency: Monitoring OTIF scores provides insights into the performance of your supply chain. It helps identify exactly where issues lie if any problems occur. This allows you to address the right areas to optimize efficiency and minimize costs. For example, you might need to hire new staff, improve certain processes, and more.
- Enhanced reputation: Build a strong reputation for your business. Customers tend to prefer companies with efficient services, which fosters greater loyalty. The higher your OTIF scores, the more positive an image you create.
- Competitive advantage: Excelling in OTIF performance can position your business as a formidable contender in the market. Satisfying customers, your business reputation will improve, leaving a stronger impression on them.
The benefits of high OTIF: Boost your business performance
Read more >>> Order Processing – Definition, Benefits, 7 Step Order to Process
Strategies to improve OTIF
Improving OTIF is often a challenging issue for many. However, strategies to improve OTIF in manufacturing can help optimize processes and minimize costs.
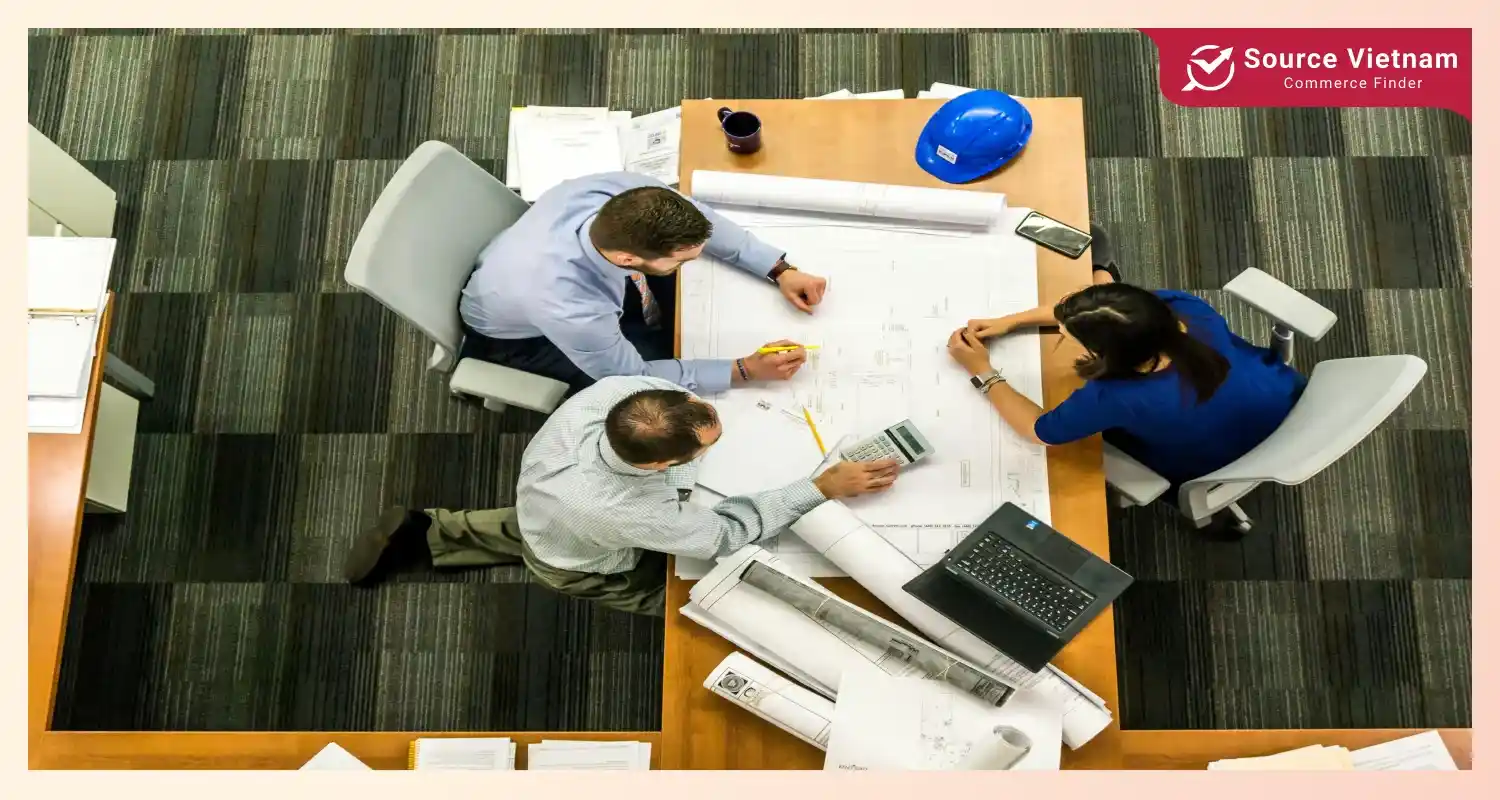
Demand forecasting
Accurate demand forecasting plays a crucial role in managing inventory effectively, making it an essential strategy for businesses to prioritize. It helps suppliers anticipate requirements and plan more effectively for successful deliveries.
Inventory management
Effective inventory management is essential as it significantly impacts a business’s stock levels. If inventory runs out, delivering orders to customers becomes challenging. Therefore, good inventory management reduces the risk of stockouts and minimizes late deliveries to customers.
Production planning and scheduling
Proper production planning is essential. If the production schedule does not align with demand forecasts, your business is highly likely to face stockouts. Conversely, if well-coordinated, the likelihood of meeting delivery deadlines increases.
Transportation and logistics optimization
Transportation and logistics management is essential, with strategies including:
- Route optimization.
- Appropriate carrier selection.
- Optimizing warehouse activities.
- Technology adoption and more.
Order fulfillment process improvement
How can order fulfillment processes be simplified? The answer lies in appropriate technologies and approaches. This will help minimize delays in order placement and delivery. However, careful consideration is needed to determine the most suitable strategy.
Supplier collaboration
Ensure punctual delivery of raw materials and a wide range of components by suppliers. Businesses must maintain strong relationships with them. Good collaboration helps minimize delays and reduces the likelihood of supply chain issues.
Technology and automation
Pay attention to technology and automation. Implement programs and software to manage the supply chain more effectively, such as platforms for real-time tracking.
Some recommended management systems include:
- ERP.
- OMS.
- eCommerce platforms.
- WMS.
- CRM systems.
- TMS and more.
Boost your OTIF score with these proven strategies
Common challenges in achieving high OTIF rates
Having a high OTIF score is always a goal that businesses strive for. However, attention must be paid to certain issues that can create significant challenges.
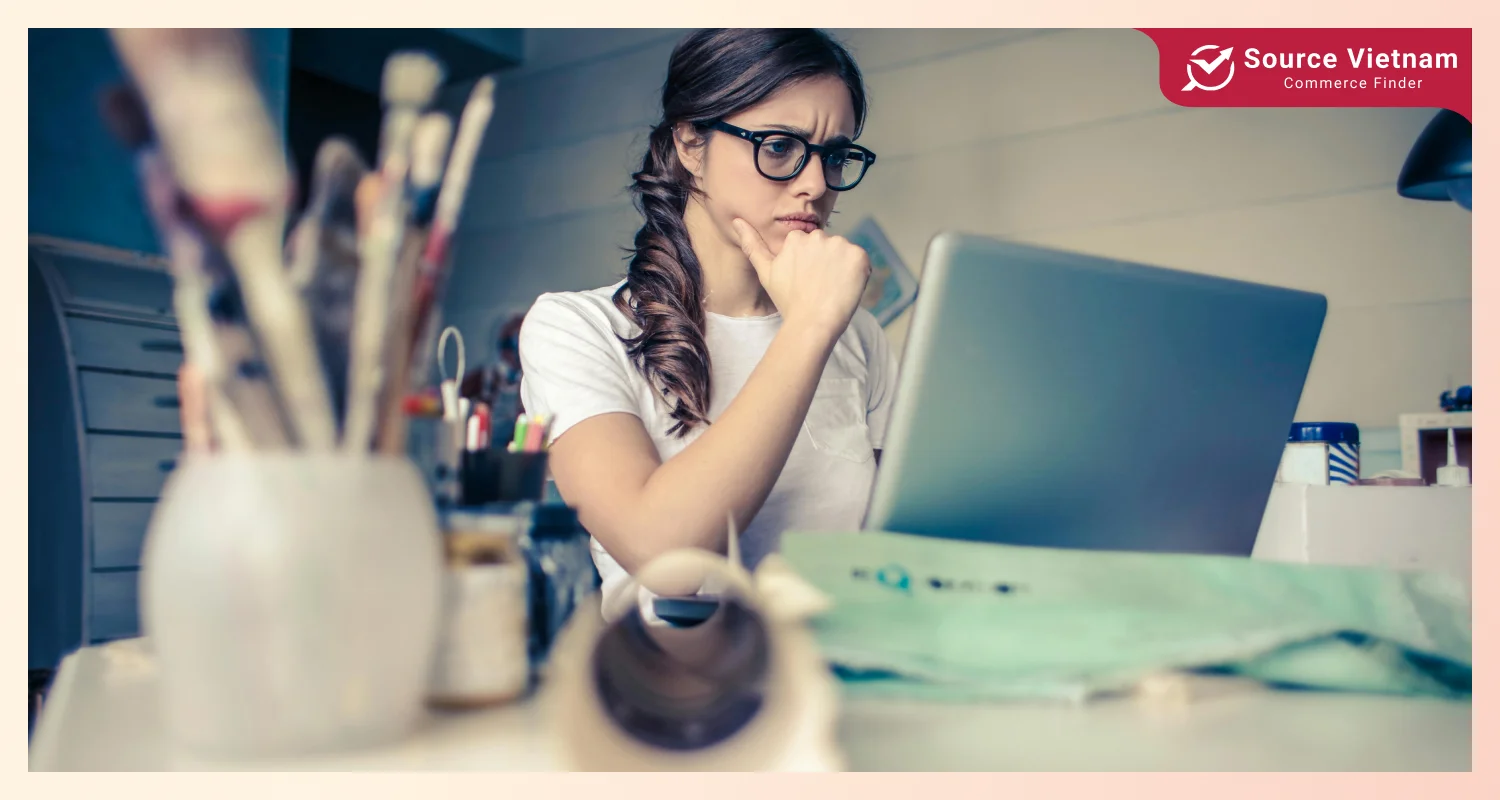
Inaccurate demand forecasting
Demand forecasting impacts a business’s inventory levels. If a business inaccurately forecasts demand, deliveries will not proceed smoothly, resulting in low OTIF performance. Therefore, demand forecasting plays a crucial role in improving OTIF scores.
Supply chain disruptions
On-time delivery is ideal, but unforeseen issues like natural disasters can impact it. Other disruptions, such as port closures, traffic congestion, accidents, and bad weather, can also prevent OTIF from meeting expectations.
Consider Procter & Gamble. In 2017, as Hurricane Irma approached Florida, they used scenario planning to assess the potential effects on their supply chain. They ran multiple simulations and even outlined actions to take if the hurricane’s path shifted. This ensured that customers could locate their goods after the storm.
Lack of visibility
Ensuring end-to-end visibility across the supply chain and keeping track of order progress is no small feat.
Inefficient processes
Inefficient order fulfillment processes can lead to delays. Production and logistics issues also require attention as they directly impact deliveries.
Overcoming OTIF challenges: A practical guide
OTIF benchmarks and industry examples
Check out the next section to explore OTIF benchmarks and real-world industry examples.
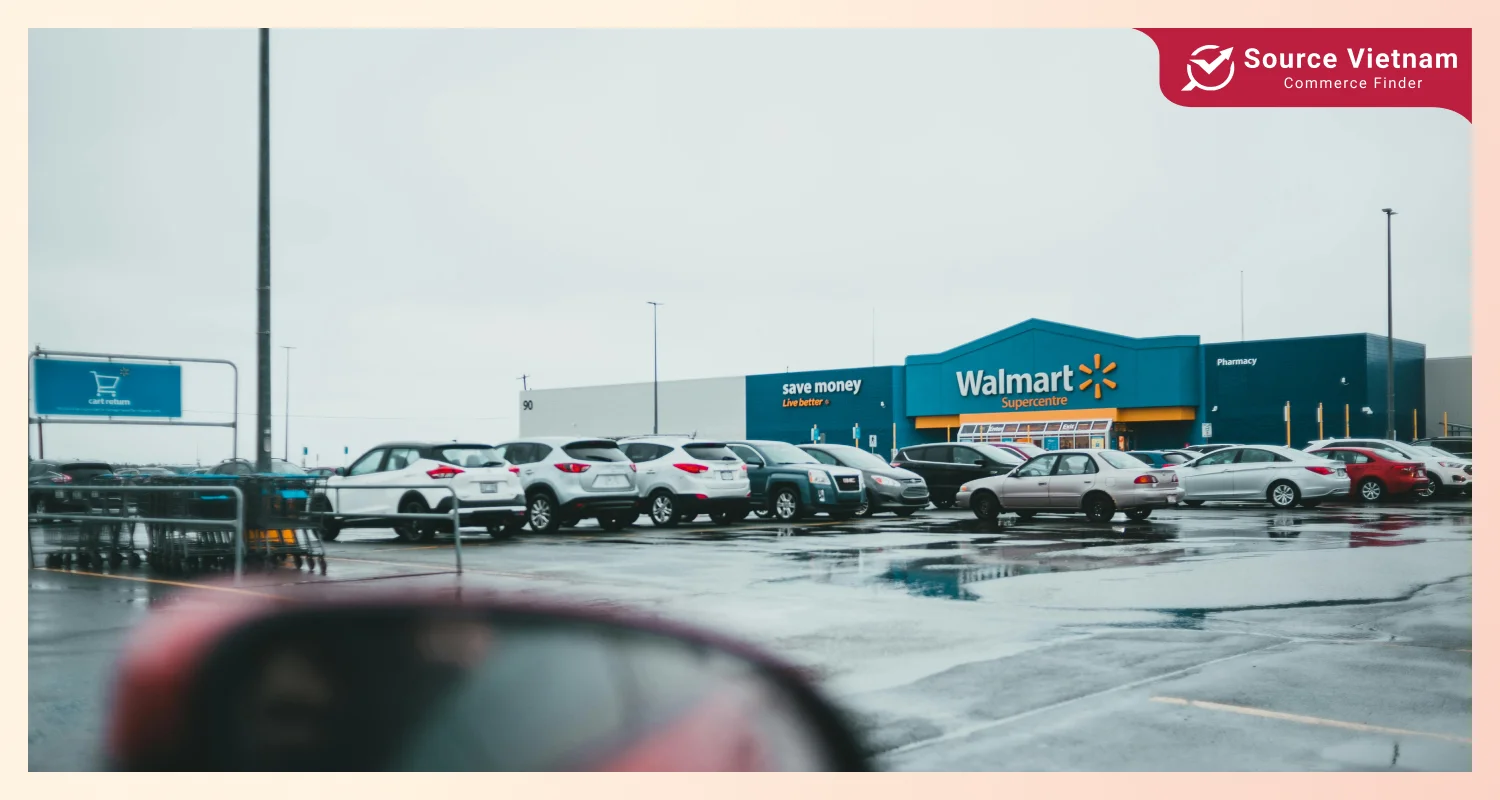
In summary, OTIF benchmarks can exhibit significant industry-specific differences. For example:
- In eCommerce and consumer goods, an OTIF score of 95% or higher is expected.
- OTIF benchmarks in retail supply chains will depend on the specific business.
Take Walmart as an example: in 2020, the company aimed for an OTIF rate of 98%. More recently, these targets have shifted to 90% for on-time delivery and 95% for in-full delivery.
Walmart stands as an illustration of achieving success through the strategic application of OTIF KPIs. They leverage OTIF KPIs to identify areas for improvement within their supply chains. Specifically, Walmart uses OTIF data to improve inventory and logistics operations.
OTIF in action: Real-world examples and benchmarks
Conclusion
By exploring the OTIF meaning and how to calculate it, insights into its benefits and methods to optimize it within a business will unfold. There’s no denying that optimizing OTIF elevates customer satisfaction while sharpening your competitive edge. Tracking OTIF often brings significant benefits to businesses and helps identify core issues that need optimization to manage the supply chain more effectively.
Optimize your supply chain and achieve OTIF excellence through the information we have just provided. Discover more fascinating insights about supply chains at SourceVietnam.com.
FAQs about OTIF
What does OTIF mean in the supply chain?
This is a metric that measures supply chain performance. OTIF meaning encompasses two key aspects:
- On-Time: Ensures deliveries reach their destination within the specified timeframe as agreed.
- In-Full: Guarantees that the complete order arrives intact, with no items missing or incorrect.
How do you calculate OTIF?
Calculate OTIF using the following formula:
OTIF = (Number of orders delivered on time and in full/total number of orders) x 100
Why is OTIF important?
OTIF holds significance as it provides a comprehensive view of supply chain efficiency, customer satisfaction, and its impact on revenue. By analyzing OTIF, businesses can pinpoint issues within their operations and strategize ways to resolve them.
What are the benefits of achieving a high OTIF score?
The benefits of achieving a high OTIF score are hard to overlook. Achieving high OTIF scores brings numerous appealing advantages:
- Enhanced customer reliability.
- Reduced costs.
- Improved performance.
- Boosted reputation.
- Competitive edge in the market.
What are some common challenges in achieving high OTIF?
Aiming for a high OTIF score is an aspiration shared by many businesses, but reaching this target demands tackling challenges like:
- Inaccurate demand forecasting.
- Supply chain disruptions.
- Lack of visibility.
- Inefficient processes.