Cost of production is total cost incurred by any business in manufacturing any good or providing any service is referred to as a cost of production. It includes various types of expenses, namely, manufacturing maintenance, labour expenses, freight expenses, and raw materials costs. Production costs include the state and federal taxes levied on a manufacturing facility or any manufacturing process.
The cost of production is an important consideration in a business’s manufacturing or production processes. It usually covers labour costs as well as the supplies and raw materials a business uses during production.
Knowing how to calculate, report, and control the cost of production is a way to determine if the products of a company are lucrative and profitable.
This article defines what “cost of production” means, describes the many types of production costs, and provides the variables that affect the cost of production for a company.
What is cost of production?
Production cost is one kind of expense that is crucial to the upkeep of industrial operations and the growth of a company. Let’s find out the answer to the question: “What is production cost?” below.
- Definition: The total cost incurred by any business in manufacturing any good or providing any service is referred to as a cost of production. It includes various types of expenses, namely, manufacturing maintenance, labour expenses, freight expenses, and raw materials costs. Production costs include the state and federal taxes levied on a manufacturing facility or any manufacturing process.
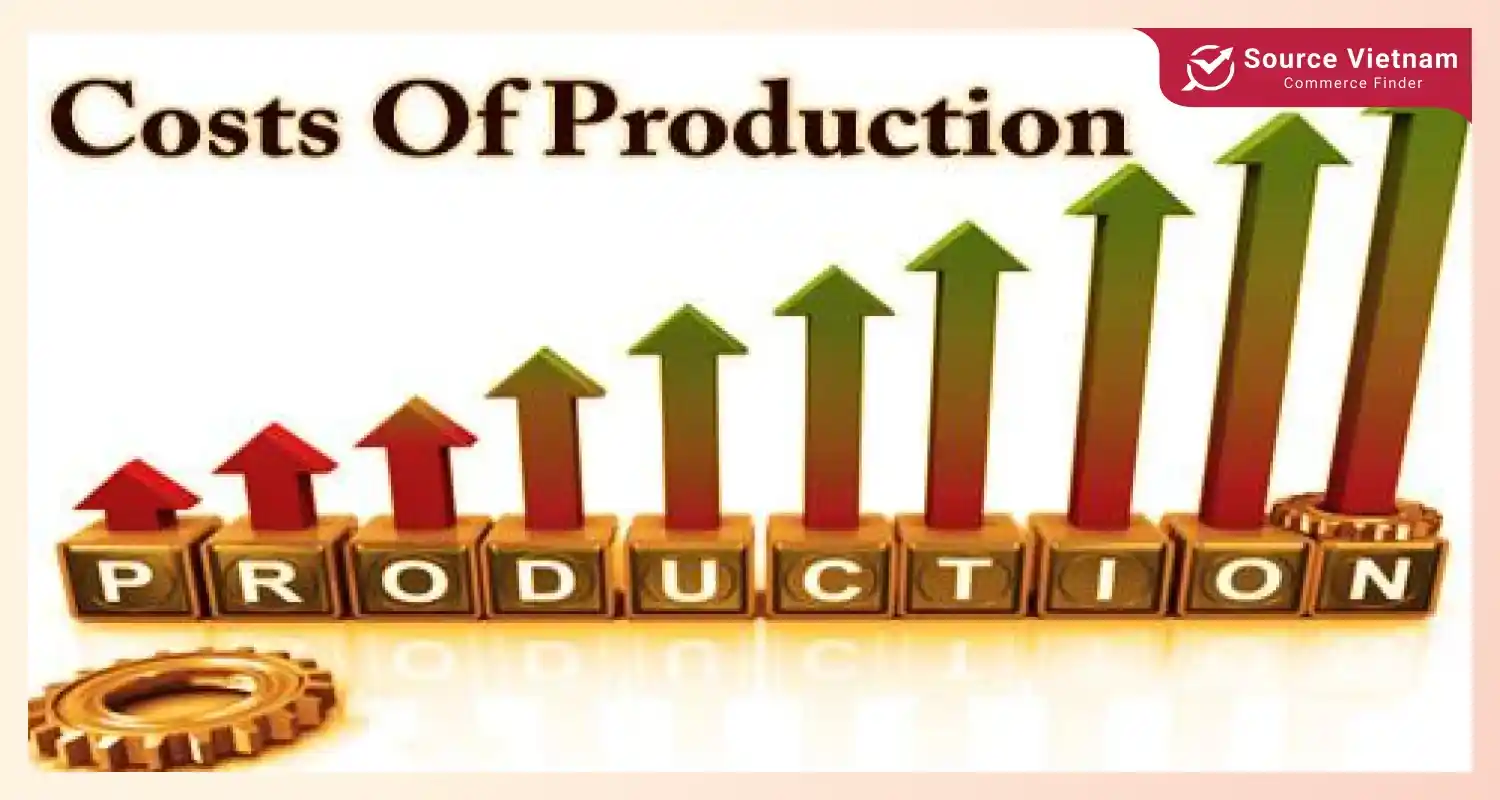
- Components: Main production costs include direct materials (raw materials used to produce the product), direct labour (wages for people directly involved in producing the product), and manufacturing overhead-just about all other indirect costs (like rent and utilities) that support production. The sum of these costs is the total cost of producing goods or services.
- Importance: Production costs help outline profitable pricing, analyze profit margins, and control expenditure. This enables companies to pinpoint their operational inefficiencies, analyze the profitability of the products manufactured, and provide them with competitive pricing, enabling them to reduce their costs and improve their financial performance in the overall market.
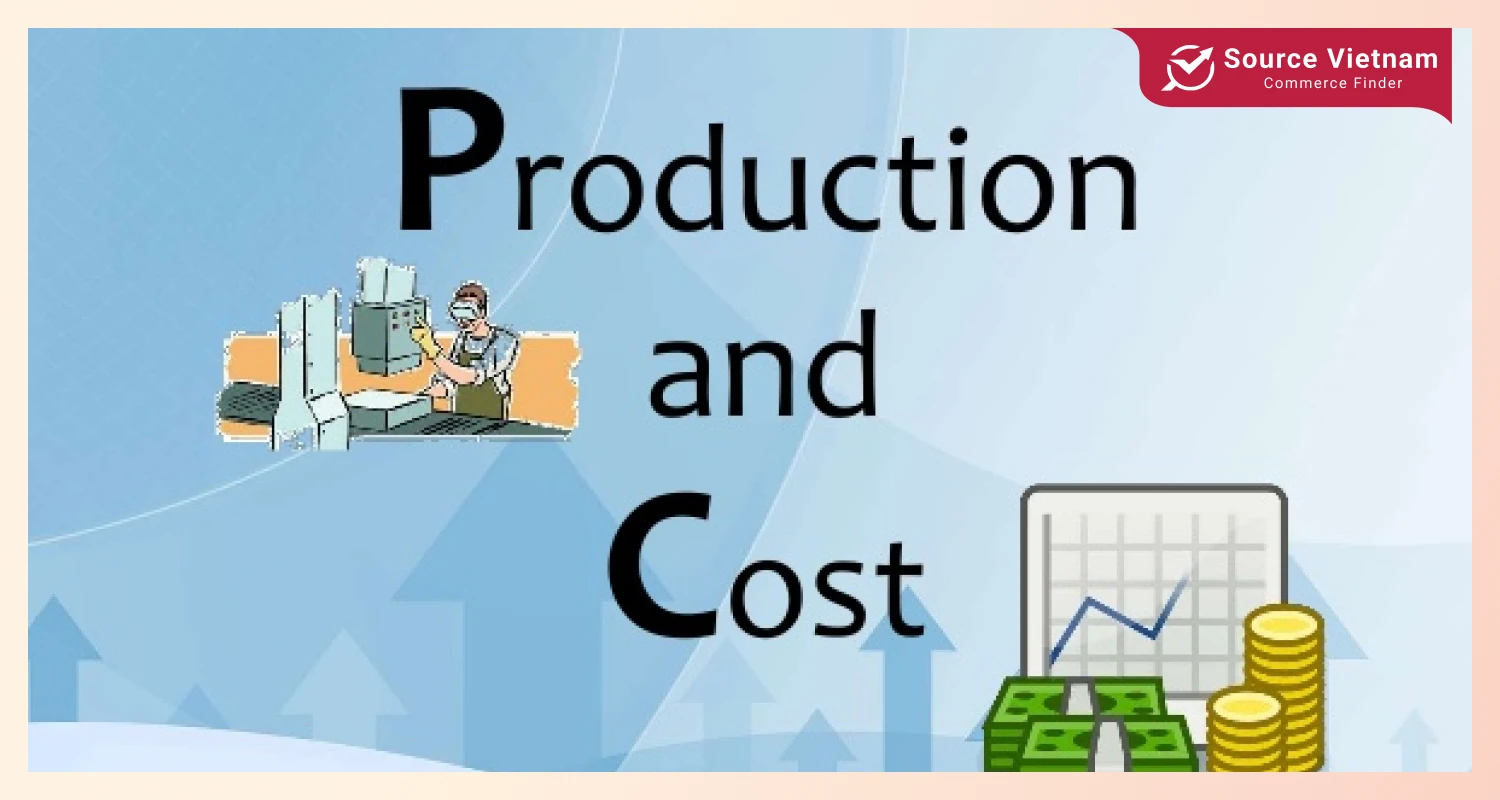
Cost of production explained: Essential for business owners.
Read more >>> Cost of Goods Sold (COGS) – Definition | Type | Calculation & Importance
Types of production cost
Businesses can better comprehend the structure and proportion of costs included in cost of production type that must be spent within a specific timeframe by classifying production expenses according to their economic nature, including, in particular:
- Fixed costs:
- Definition: These expenses are those that remain constant regardless of the volume of output or economic activity. These expenses don’t change based on production or sales volume.
- Examples: Rent, insurance, and salaried workers are a few examples. Even in the event that the business generates nothing, fixed expenditures are incurred.
- Variable Costs:
- Definition: Expenses that vary directly with the volume of production or company activity are known as variable costs. These expenses rise with rising production and fall with falling production.
- Examples: Raw materials, direct labour, and utility expenses that change according to output volume are examples.
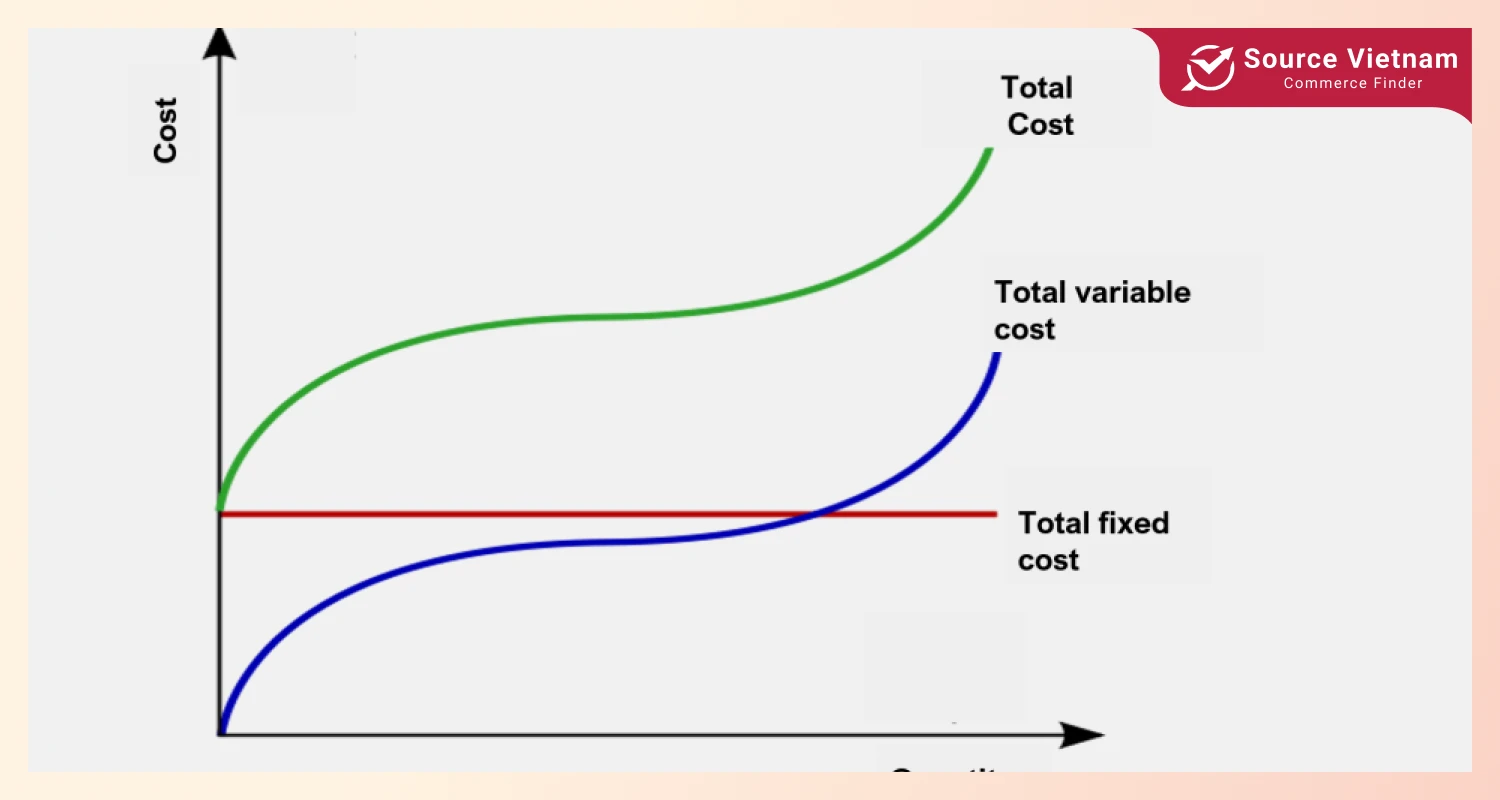
- Direct Costs:
- Definition: These costs are expenditures that have a clear link to the creation of a particular good or service.
- Examples: These charges cover direct labor, raw accouterments, and any fresh charges directly related to producing a certain good.
- Indirect Costs:
- Definition: These are costs not directly attributed to the product of a particular good or service. Though they do not contribute to producing a particular point, they contribute to the whole process of product.
- Examples: Rent, utilities, administrative pay, and equipment upkeep are a few examples. Usually, indirect expenses are distributed over several goods or services.
Breaking down production costs: Fixed, variable, direct, and indirect.
Read more >>> Profit margin calculation
Calculating cost of production
You’ll need to add up all the charges involved in the product of goods or services to get the cost of product. The general formula to calculate the cost of product looks like this:
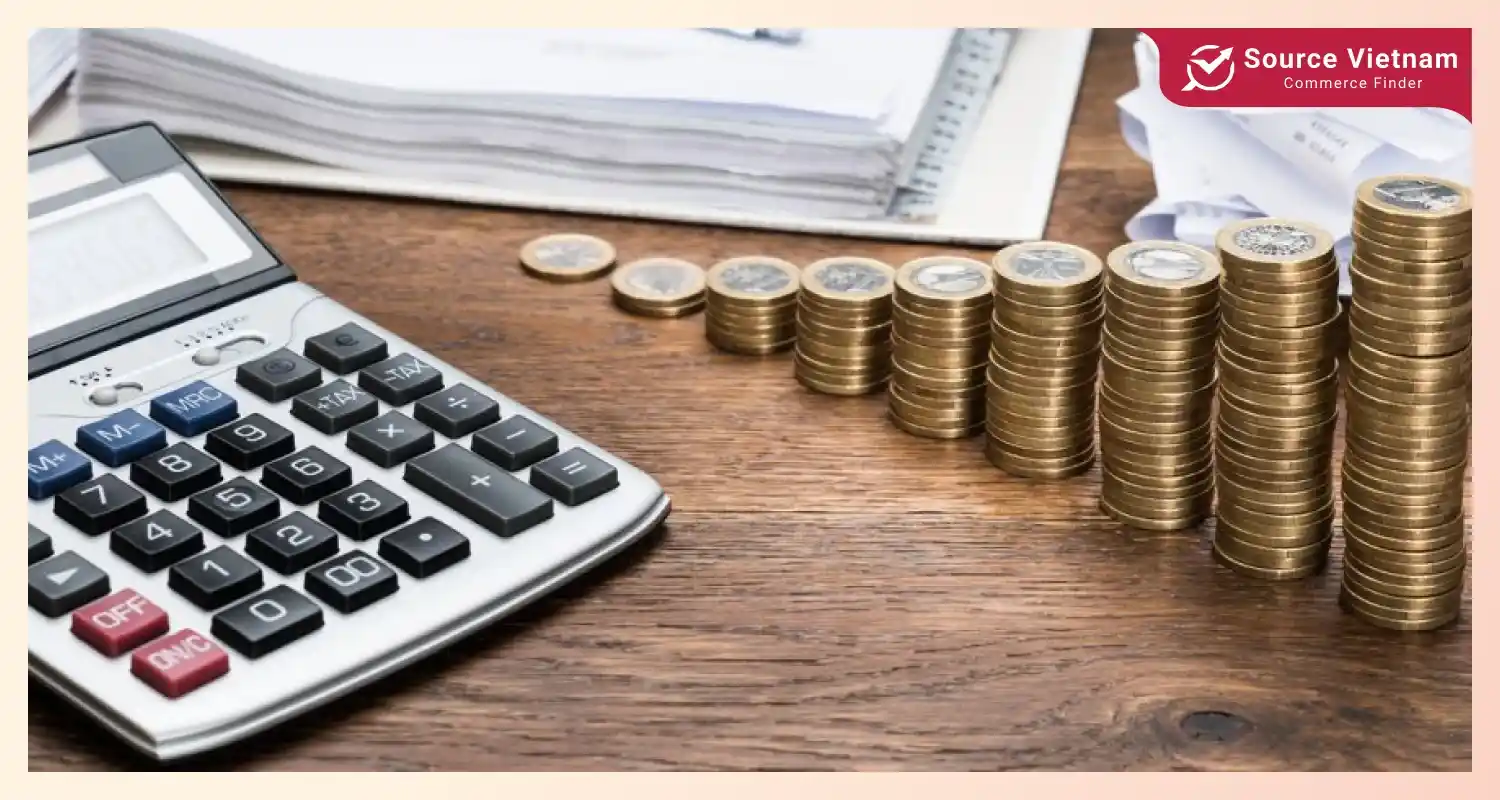
Formula:
Total Production Cost = Direct Materials + Direct Labor + Manufacturing Overhead
- Direct materials cost calculation: When calculating direct accoutrements costs, one must take into account the accoutrements employed, the unit cost of accoutrements, and the waste or scrap produced during the product process.
- Quantity used: This is the quantity of raw materials required throughout the manufacturing process. Although it is measured in numbers like kilos, liters, or meters, this usually depends on the kind of substance.
- Unit cost: The price of one unit of each raw material is referred to here. Market conditions, supplier agreements, and purchasing volume could all have an impact.
- Waste or scrap: Materials that are not utilized in a final product because of flaws, excess, or industrial inefficiency are referred to as waste or scrap.
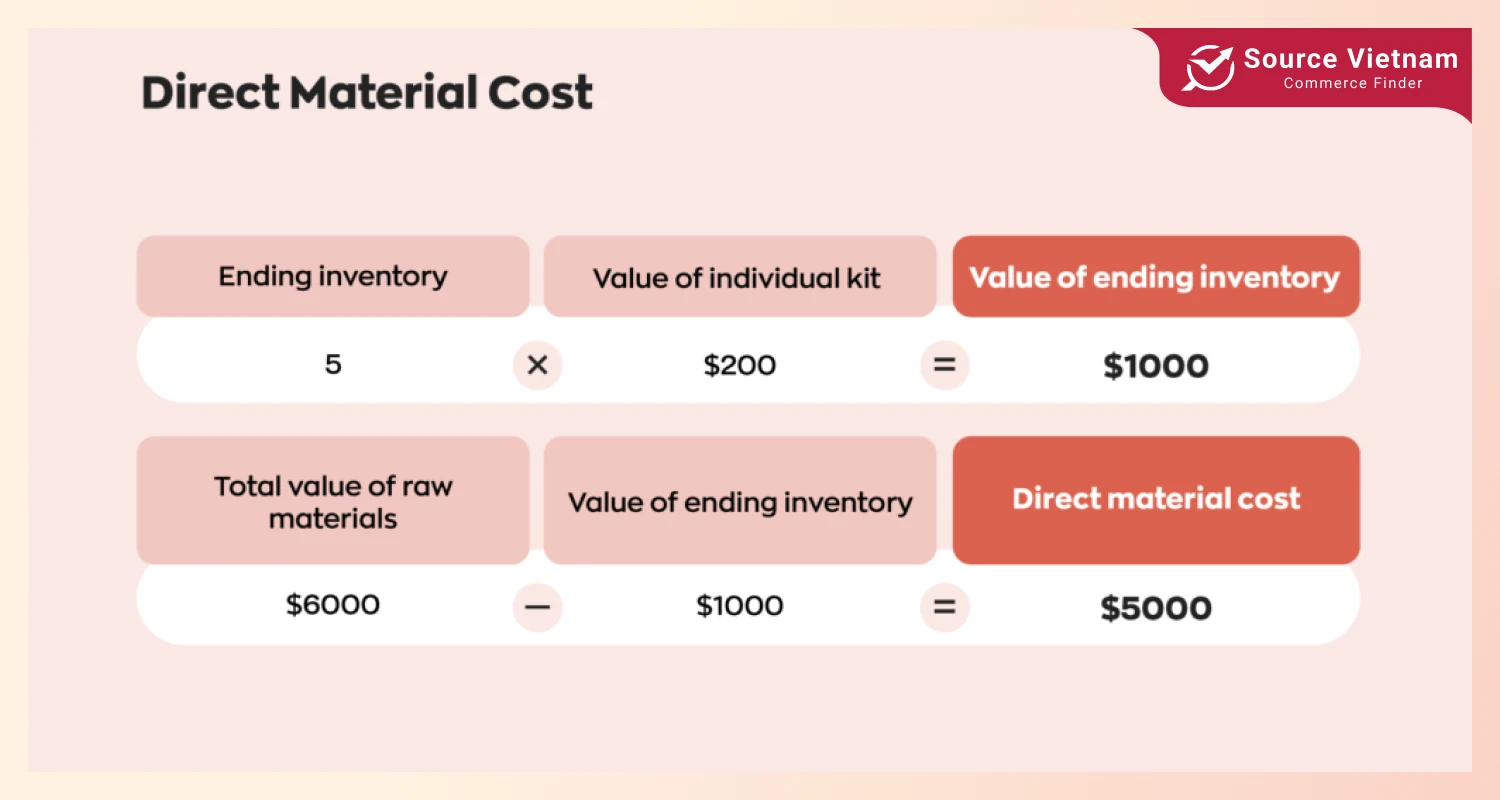
The formula for direct materials costs:
Direct materials cost = (Quantity used × Unit cost) + Cost of waste or scrap
Let’s assume a factory consumes 500 raw materials, each costing $4. Fifty units of material, or 10% of the total, are wasted or scrapped during manufacture. Since scrap was originally acquired, its cost is factored into the overall computation. Step-by-step calculation:
Step 1: Determine how much the materials used will cost:
Cost of used materials = 500 × 4 = 2,000
Step 2: Determine the scrap’s cost:
Cost of scrap = 50 × 4 = 200
Step 3: Total cost of direct materials:
Direct materials cost = 2,000 + 200 = 2,200
Calculate your production costs: A step-by-step guide.
Per unit cost of production
The per unit cost of production indicates the total cost involved in production to create a single unit of any product, which is the total number of units produced divided by the summation of direct and indirect costs, comprising direct labour, direct material, and manufacturing overhead. Let’s see in detail how to calculate per unit cost of production and formula for per-unit production cost below.
- Importance: Per unit cost of production is important for price setting and profitability assessment for your business. Knowing this signal might assist your business in figuring out the lowest price required to meet costs and reach the targeted profit margins. Businesses can assess the profitability of their pricing strategy and whether lowering manufacturing costs is necessary to boost financial performance by comparing selling prices to unit expenses.
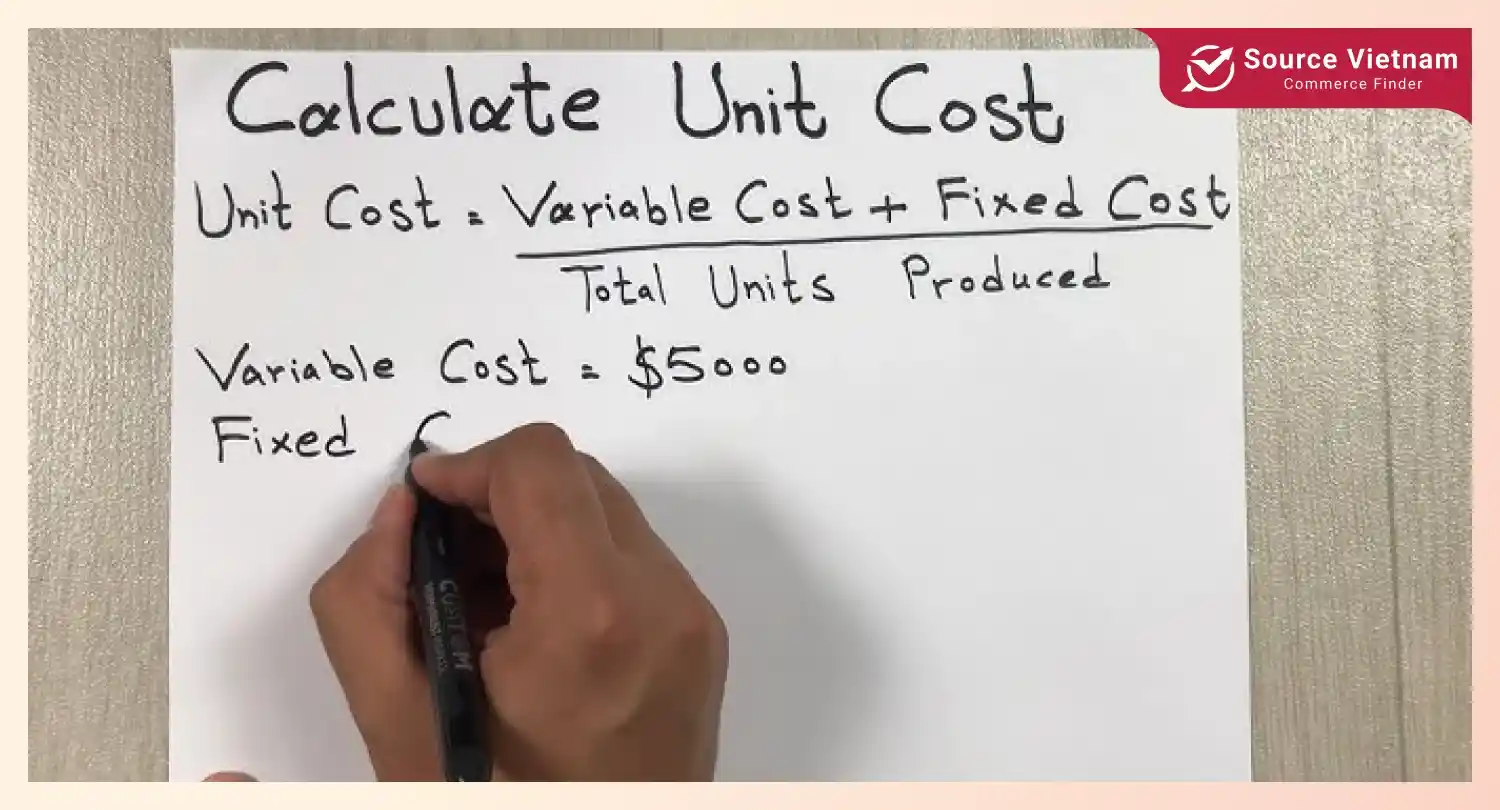
- Per unit cost of production formula:
Per unit cost of production = Total production cost / Number of units produced
Example: Total production costs: $10,000 (including materials, labour, and overhead); Total units produced: 1,000 units.
Per unit cost = 10,000 / 1,000 = 10
In this instance, the production cost per unit is $10.
Calculate your per-unit production cost for better pricing.
Period cost vs. Product cost
Two important cost categories in accounting are period costs and product costs, each of which has a distinct function in financial reporting and decision-making. The difference between period and product cost is as follows:
Criteria
|
Product costs
|
Periods costs
|
Definition
|
Costs tied to production.
|
Costs not related to production.
|
Components
|
Direct materials, direct labor, manufacturing overhead.
|
Selling, general, and administrative expenses (SG&A).
|
Treatment
|
Capitalized as inventory, expensed when sold.
|
Expensed in the period incurred.
|
Example costs
|
Raw materials, wages, factory rent
|
Office rent, marketing expenses
|
Impact on financials
|
Included in COGS and inventory.
|
Expensed on the income statement.
|
- Detailed comparison: Production expenses – costs linked to specific products, such as labour, materials, and overhead, are directly related to product costs. They are capitalized as inventory and expensed upon sale. Examples of period costs that are not associated with production and are subtracted at the time of occurrence are selling and administrative expenses. The main distinction is that period expenses are instantly expensed, whereas product costs are included in inventory and cost of goods sold.
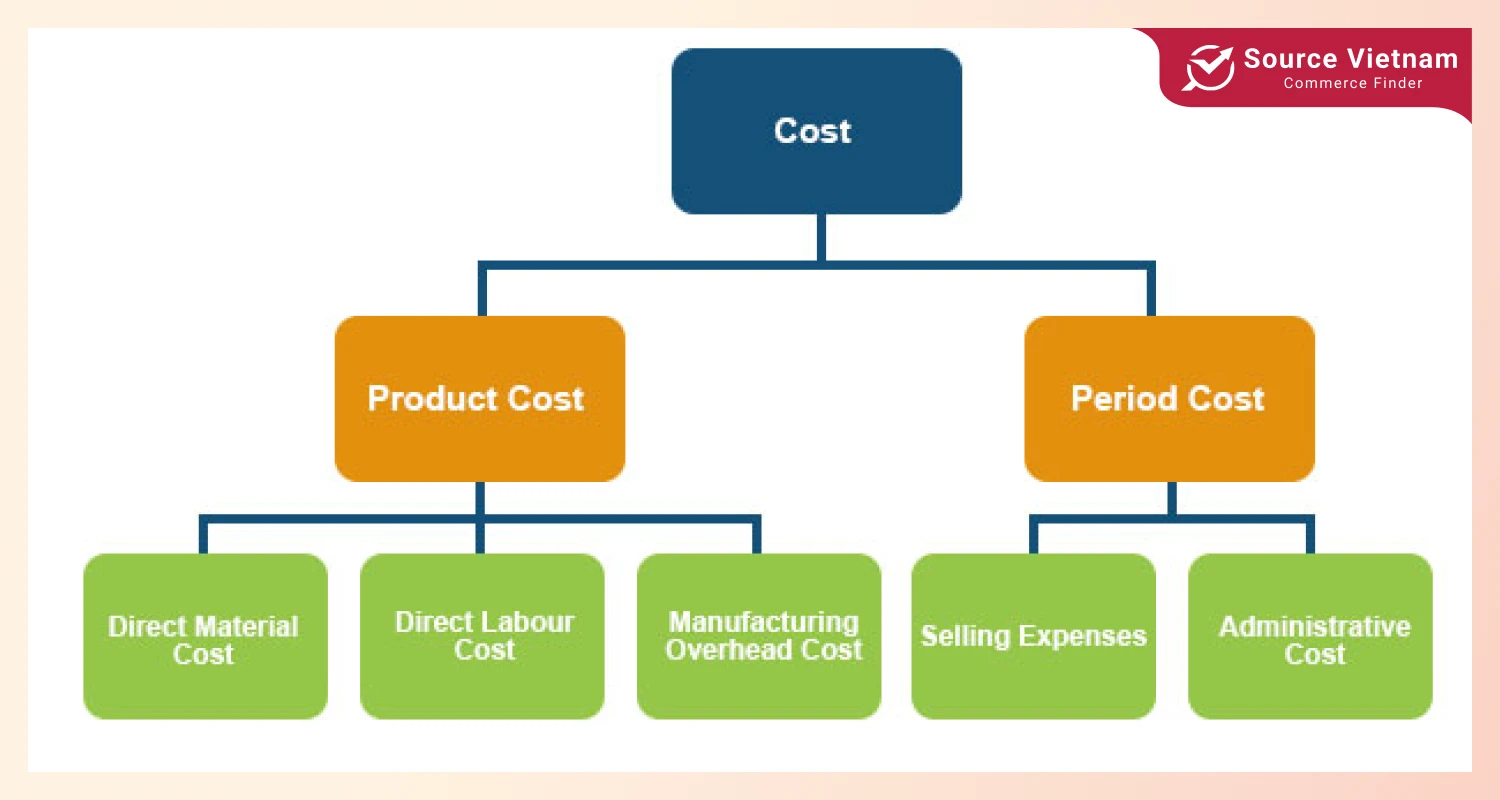
- Importance of classification: Financial reporting, inventory valuation, and cost tracking all depend on accurate cost classification. It guarantees that inventory is valued appropriately, expenses are distributed appropriately, and financial statements accurately depict actual profitability. This aids companies in maintaining compliance, making well-informed decisions, and presenting a transparent financial picture.
Period costs vs. Product costs: Understanding the difference.
Advanced costing methods
Beyond conventional costing methods, advanced costing approaches offer more precise and thorough insights into production costs, assisting firms in making better decisions. Among the main advanced costing techniques are:
- Activity-based costing (ABC): This strategy allocates expenses to products or services after being assigned to activities depending on how they consume resources. By taking into account the exact activities that generate expenses rather than applying them generally, it gives a more realistic view of overhead costs.
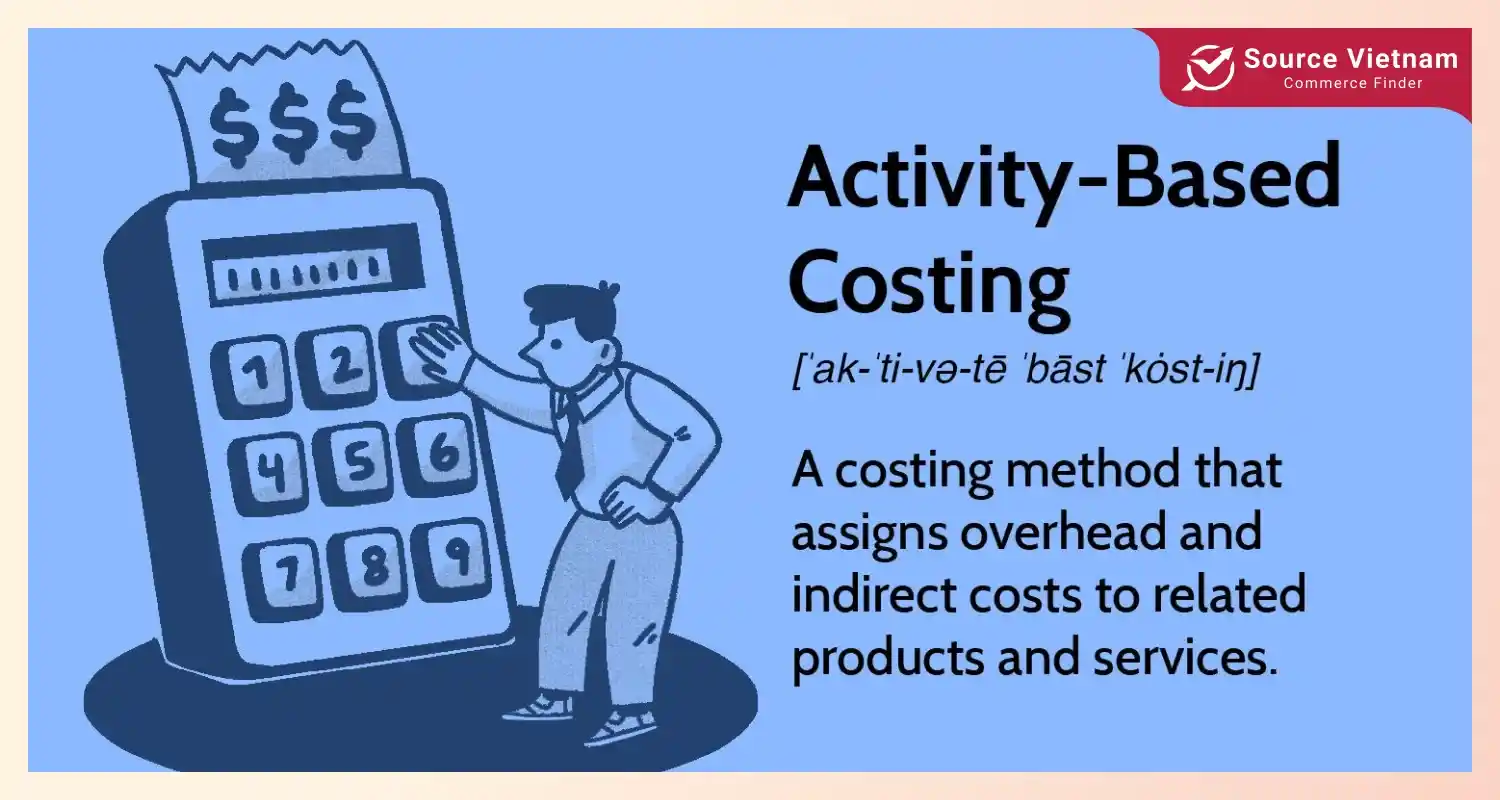
- Standard costing: This entails establishing fixed prices for labour, supplies, and overhead and then contrasting actual expenses with these benchmarks. To increase efficiency and regulate performance, differences between standard and actual costs are examined.
- Optional: In addition, there are various costing techniques like lean accounting and cost-volume-profit analysis. These cutting-edge techniques give cost allocation greater accuracy, assisting companies in increasing pricing, profitability, and overall operational effectiveness.
Conclusion
Direct labour, direct materials, and manufacturing overhead are all included in production costs. They are separated into two categories: variable costs, which vary according to output, and fixed costs, which remain constant during production.
While indirect expenses assist production but cannot be precisely traced, direct costs are associated with it. Pricing, profitability, and cost control are all aided by the computation of production costs.
Businesses can increase profitability, find cost-saving opportunities, and set more competitive prices by comprehending and evaluating manufacturing costs.
If you are a business owner or have a passion for business, please visit SourceVietnam.com to assess your gross profit better, optimize pricing strategies, and identify areas for cost control.
FAQs about cost production
What are the different types of production costs?
The primary categories of production expenses are:
- Direct costs include the cost of raw materials or direct labour associated with commodity manufacturing.
- Indirect costs include factory rent, utilities, and other expenses that support manufacturing but cannot be directly traced to a product.
- Fixed costs are those that do not change with the rate of production, such as salaries of labour and depreciation of equipment.
- Variable costs are those that vary directly with production levels, such as raw materials and hourly labour.
- Semi-variable costs: It includes both fixed and variable cost elements, like a basic pay plus commission.
These kinds assist companies in monitoring, managing, and maximizing their production-related costs.
How do I calculate the cost of production for a service?
To calculate the cost of production for a service, add direct costs (for example, labour and materials) and indirect costs (for example, rent and utilities). The cost of service is calculated as follows:
Production Cost = Direct costs + Indirect costs
What factors can affect my production costs?
The price of raw materials, labour costs, overhead, supply chain problems, production size, and regulatory changes are some of the variables that might impact production costs. These elements have the power to affect profitability by raising or lowering total costs.
How can I reduce my production costs?
To lower production costs, raise productivity, negotiate the prices of vendors, reduce wastage, automate a task/outsourcing of the task and utilize available manpower, installing energy-saving facilities.
What are fixed and variable costs?
Rent, salaries, and equipment depreciation are a few examples of fixed expenses independent of production volume.
Raw materials, direct labour, and energy consumption are a few examples of variable expenses that change in direct proportion to the volume of output.
In conclusion, variable costs rise or fall in response to production volume, whereas fixed costs remain constant regardless of output.